Types of Blown Film Extrusion Machines : Choosing the Right Fit
The applicability of blown film extrusion machines is very wide, and there are different specifications of blow film machines for various purposes. Whether it is a higher-tech three-layer blow film extruder or a high-quality single-layer blow film extruder, each variant has its specific role in the plastics industry. This piece delves into the features, applications, and benefits of different blown film extrusion machines, providing valuable insights for manufacturers and industry enthusiasts looking to find the perfect fit for their specific needs.
Blown Film Extrusion Process
The blown film extrusion process is a highly efficient method of manufacturing films. It involves melting plastic resin in an extruder, which is then blown into a bubble using air. The bubble is cooled, flattened, and wound into rolls. This process ensures uniform thickness and excellent material properties, making it suitable for producing packaging films, agricultural films, and more. The process parameters, such as temperature, cooling rate, and blow-up ratio, play a crucial role in determining the film's quality.
1.Multi-Layer Blown Film Extrusion Machine
These machines are characterized by incorporating multiple extruders, capable of producing multi-layer structures ranging from two layers to up to nine or even eleven. Each layer could be made of different materials providing variations in physical properties, capabilities, and cost-efficiency. Multi-layer blown film machines are useful for producing heavy-duty packaging bags for industrial applications due to the superior strength and durability their products offer. One of the most common types of multi-layer blown film extrusion machines for plastic bags is 3 layer blown film machines.
Three Layer Blown Film Machines
-
ABC Blown Film Machine(JC-3CX Series)
Enhanced Performance with Three-Layer Blown Film Machine
The three-layer blown film machine is distinguished by its ability to amalgamate the advantages of three distinct types of plastic materials, resulting in a film with improved strength performance , barrier properties, gloss, and more. The applications of the three-layer blown film machine are extensive, encompassing packaging, construction, and industrial sectors. In the packaging industry, it can manufacture diverse products such as food packaging, industrial packaging, agricultural packaging, and more. In the construction sector, it is produced for the production of construction film, waterproof film, while in the industrial domain, it contributes to the manufacturing of printing film, thin films for wires and cables, and other applications.
Material Input Handling : Auxiliary Equipment Selection
When it comes to selecting peripheral equipment, such as the material feeding system, it is advisable to opt for a high-precision dosing system. This system is designed to automatically calculate and blend various raw materials and additives to meet the specific characteristics required for the final product. The selection of the air ring involves choosing advanced automatic control air rings, complemented by an automatic film thickness measurement system to closely monitor the production process. Additionally, this machine recommends the incorporation of an oscillating take-up device for achieving uniform film thickness.
Efficient Production for Automatic Winding
Given the machine's capability to produce wider films (with a maximum recommended width of 2500mm), an automatic winding system is recommended. This winder should feature a digital tension controller, automatic roll changing , and hydraulic unloading system to enhance overall production efficiency.
-
ABA Blown Film Machine(JC-2CX Series)
Maximizing Flexibility and Efficiency
The ABA blown film machine stands out as a three-layer co-extrusion apparatus, incorporating two extruders that independently feed diverse materials into the die head. The outer and inner layers are crafted from the same material, while the middle layer comprises a distinct material. The features of ABA blown film machine is more flexible than single layer blown film extruders. The extruder of the B layer is allowed for the inclusion of special raw materials, recycled materials, or calcium carbonate in the B layer. This adaptability is by customer requirements or economic considerations. The middle layer can accommodate up to 50% calcium carbonate or recycled materials, resulting in a significant reduction in the consumption of new materials and, consequently, a substantial decrease in production costs.
Enhanced Strength and Efficiency in ABA Films
The film strength and thickness of ABA films surpass films produced by single-layer blown film machines. Despite the initial higher mechanical cost, ABA demonstrates long-term economic benefits due to the decreased expenditure on raw materials. ABA films find diverse applications in sectors such as food packaging, industrial packaging, agricultural packaging, and more.
Read also:3 Key Upgrades in 3 Layer Blown Film Machines for Superior Performance
2.Single Layer Blown Film Machines
Mono-layer blown machines are the basic machine of blown film lines. They are ideal for manufacturing general packaging bags, which include supermarket and grocery bags. For start-ups and long-term stabilized manufacturers, this machine offers a profitable and cost-effective solution.
-
HDPE/PP Monofilament Extrusion Line(JC-HS Series)
Optimal for Efficiency and Quality
The HS high-speed blown film machine is a frequently selected single-layer apparatus, well-suited for high-output and high-quality film production. Capable of manufacturing films with widths ranging from 500 to 1200mm, it is primarily utilized for the production of vest bags, packaging bags, garbage bags, shopping bags, and various plastic bags.
Versatility in Film Production : HS Model Features
The HS model offers versatility through die head and air ring replacement, allowing the choice between producing HDPE or LDPE films. This flexibility caters to a range of film applications. The adjustable lifting structure accommodates cooling times of different materials, effectively minimizing the occurrence of undesirable film wrinkles.
Customized Winding Solutions : Enhancing Production Efficiency in HS Model
When it comes to selecting winders in the HS model, the choice is influenced by the intended use of the product. Options include single or back-to-back winders, and customers typically opt for automatic or manual winders based on their preferences. Additionally, there is the option to incorporate automatic air knife film cutting and automatic unloading system, enhancing overall production efficiency.
-
Single-Layer LDPE High-Speed Blown Film Machine
Precision in LDPE/LLDPE Film Production (LH Series)
The LH series of blown film machines is dedicated to the production of LDPE/LLDPE films, ensuring both high output and superior film quality. Capable of manufacturing films with widths ranging from 1000 mm to 3000 mm, it proves ideal for the production of packaging bags, shopping bags, and more.
The machine structure of LH series is not adjustable, featuring a higher frame designed to accommodate LDPE/LLDPE raw materials requiring longer cooling times. The fixed structure, while limiting adjustment, provides stability crucial for the production process. The wider film range further enhances its versatility, making it suitable for an array of bag sizes.
Customized Winding Solutions for Enhanced Efficiency
When selecting winders for the LH model, the choice is guided by operating habits and production requirements. Automatic winders are recommended, particularly for windingfilms, to optimize production efficiency. This strategic choice ensures an efficient winding process, contributing to the overall effectiveness of the LH High-Speed Blown Film Machine.
-
Compact Single-Layer Blown Film Machine (JC-HM series)
The HM model stands as the smallest blown film machine, proficient in producing films with widths ranging from 350mm to 600mm. Designed for the manufacturing of economical and smaller bags or shopping bags, this compact machine excels in space efficiency, simplicity of operation, and overall convenience. It proves to be an ideal choice for initial users prioritizing ease of operation or engaging in the bags production line.
-
PP Blown Film Machine(JC-PB Series)
Superior PP Film Quality through Water Cooling
Unlike traditional blown film machines that use cold air for film cooling, the PP blown film machine utilizes a downstream water cooling. Given the high thermal stability and heat resistance of PP's thermoplastic nature, swift cooling during the film blowing process is crucial to prevent shrinkage or deformation. Water cooling provides excellent heat transfer, quickly cooling PP films, and ensuring superior film quality. This proves especially vital in applications such as clothing packaging bags.
-
Twin-Head Blown Film Machine (JC-TH Series)
Amplifying Efficiency and Adaptability
The twin-head blown film machine incorporates two extrusion heads, enabling simultaneous production of two different films suited to various applications. Compared to single-layer machines, twin-head machines offer several benefits, such as increasing production capacity, enhancing quality, and greater flexibility. The ability to make single-layer, co-extruded, and multi-layer films makes the twin-head blown film machine a versatile and efficient option for manufacturers with diverse and changing needs.
Applications of Blown Film Extrusion Machines
Blown film extrusion machines are used across various industries, including:
- Packaging:Food packaging, industrial packaging, shopping bags, and more.
- Agriculture:Greenhouse films and mulching films.
- Construction:Waterproofing and protective films.
- Industrial Uses:Films for printing applications and laminations.
Plasco's 40 Years of Excellence: Leader of Blown Film Extrusion
Selecting the right blown film extrusion machine, an essential step for meeting production needs and future growth, requires careful consideration of your business model and market conditions. This will ensure a valuable long-term return on your investment. An optimal choice would be plastic bag blowing machines from Plasco, a globally recognized Taiwanese manufacturer with over 40 years of expertise in blown film extrusion machinery manufacturing. Known for customized solutions and professional after-sales service, Plasco stands out with its commitment to technological innovation, offering improved product performance and production efficiency. With Plasco, your investment extends beyond a high-performance machine - it's an investment in a future-focused company that always places your interests first. If you would like to learn more about how we can design and manufacture plastic bag blowing machines for your project, please contact us today !
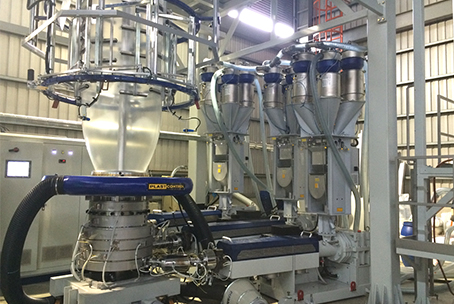
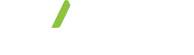
Taibao City, Chiayi County 61251, Taiwan
Phone: +886 5 2376175
E-Mail: [email protected]