How PLASCO’s Plastic Extrusion Machines Drive Sustainability and Efficiency
Championing the Circular Economy: PLASCO’s Vision for 2025
A standout focus of PLASCO’s 2025 strategy is its commitment to aligning production processes with circular economy principles. Emphasizing waste reduction and material reuse, PLASCO is championing a model that addresses the escalating global demand for sustainable practices. Our extrusion machinery supports manufacturers in shifting from traditional linear production to efficient, closed-loop systems that prioritize eco-conscious operation. Through digital integration for plastic extrusion, PLASCO’s equipment maximizes energy-saving capabilities and enhances operational efficiency, positioning the company at the forefront of sustainable innovation in the plastics industry.
Cutting-Edge Solution for Rising Energy Costs
One of PLASCO's standout innovations is its focus on energy efficiency—a crucial factor in today’s market where energy costs are unpredictable and often high. PLASCO’s advanced plastic extrusion machinery now offers impressive energy regeneration features, achieving up to 35% in energy savings. This is accomplished by converting heat generated during the extrusion process into reusable electricity, effectively powering other parts of the production line. This capability provides our clients with a considerable advantage, particularly in regions where energy costs are a major operational concern. European manufacturers have shown strong interest in this technology, as it not only curtails energy usage but also complies with Europe’s rigorous environmental standards, making it a powerful asset in sustainable manufacturing.
This project of PET plastic straps extrusion effectively showcases the reuse of recycled energy, achieving a reduction of at least 95% in energy waste.
Leading the Way in Carbon Management: Preparing for a Greener Future
In addition to its energy regeneration innovations, PLASCO is proactively addressing the growing emphasis on carbon management in manufacturing. With the introduction of carbon taxes in regions such as Europe and potentially beyond, manufacturers are facing increasing pressure to lower their carbon footprints. Recognizing this challenge, PLASCO has already begun the transformation of its facilities to be more sustainable, aiming to reduce carbon emissions across its production processes. This shift will not only support PLASCO’s own environmental goals but also enable the company to offer carbon certification to its clients. By providing this certification, PLASCO helps both primary and secondary manufacturers in the supply chain demonstrate transparency and accountability regarding their environmental impact, positioning its clients for future success in a carbon-conscious world.
PLASCO’s commitment to sustainability goes hand in hand with its focus on accuracy, efficiency, and secure operations. With over 30 years of industry expertise, PLASCO has earned consistent praise from clients for the reliability and accuracy of its machinery. The company’s adoption of advanced digital technologies has only strengthened this reputation, allowing manufacturers to achieve higher production accuracy, reduce material waste, and optimize energy consumption. The result is a seamless operation, with equipment such as its monofilament yarn making machine and strapping band making machine delivering both sustainability and dependability to manufacturers worldwide.
PLASCO: Pioneering Sustainable Solutions for a Growing Global Market
As a prominent manufacturer of blown film lines, monofilament extrusion lines, tape extrusion lines, and strapping band extrusion machines, PLASCO has solidified its role as a major force in the plastics extrusion machinery industry. Over the years, PLASCO has consistently delivered high-performance solutions that not only address the evolving demands of manufacturers but also align with the global shift toward sustainable practices.
![]() |
![]() |
At the 2024 Taipei PLAS exhibition, PLASCO unveiled its latest innovations, showcasing machinery designed to support the circular economy and drive energy efficiency—efforts further elevated by the integration of advanced digital technologies. A highlight of PLASCO's presentation was its monofilament extrusion line, a versatile technology serving a diverse range of industries, from agriculture and fisheries to consumer products, medical applications, and textiles. This adaptability is made possible by the line’s capability to process various materials, including high-density polyethylene (HDPE), polypropylene (PP), polyamide (PA) through the nylon extrusion process, and polyethylene terephthalate (PET). The flexibility to handle different materials allows manufacturers to produce tailored monofilaments suited to specialized applications, such as fishing nets, agricultural ropes, medical sutures, and textile fibers.
![]() |
![]() |
Recognizing the rising demand for efficient machinery in emerging markets, PLASCO has identified North Africa and Central Asia as key areas for growth. Both regions are experiencing rapid population increases and the rise of a new middle class, which is fueling demand for consumer goods, packaging materials, and other plastic products. Manufacturers in these regions are seeking reliable, high-performance machinery that can scale production while meeting stringent environmental and energy-saving standards. With a focus on sustainability, energy efficiency, and versatility, PLASCO’s solutions are ideally positioned to meet the needs of these rapidly expanding markets.
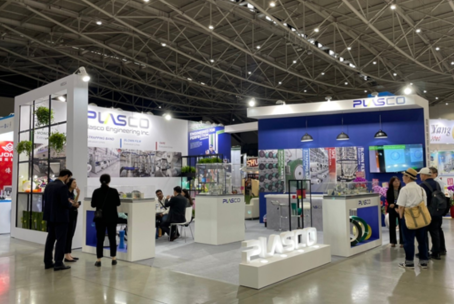
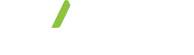
Taibao City, Chiayi County 61251, Taiwan
Phone: +886 5 2376175
E-Mail: [email protected]