A Comprehensive Guide to Monofilament Extrusion Process
Monofilament extrusion is a crucial manufacturing process used in various industries to create a wide range of products. Whether it's fishing lines, conveyor belts, brush, rope, agricultural net, or technical fiber, understanding this process is essential for anyone involved in polymer-based production. In this article, we will delve into the intricacies of monofilament extrusion, highlighting its significance and applications.
What’s Monofilament Extrusion?
So, what exactly is monofilament fiber extrusion? These fibers are typically made of various polymers, and the process involves melting the raw material and then forcing it through a specialized die to form a continuous filament with a specific diameter.
What’s the Process of Monofilament Extrusion?
The monofilament extrusion process consists of several main steps: extruding, forming, stretching, annealing, and winding. Different manufacturing processes of monofilament extrusion lines, depends on the materials used and the intended final product.
Layout of Monofilament Extrusion Line
To better understand the production process, let's look at the layout of a monofilament extrusion line.
*The layout is for reference only, the process is different depending on
material, product application, or other factors.
Monofilament Extrusion Process
1. Drying System & Material Feeding
Within the drying tower, a stream of heated air is directed upward through the ongoing cascade of granules. The capacity of the dryer must align with the required throughput of the polymer and the necessary drying time to ensure thorough drying.
2. Extruder - Melting & Homogenizing
The primary configuration for a monofilament extrusion is a single-screw design. This extruder takes the raw material in an oxygen-free environment, transports it, applies pressure, and smoothly melts it. This molten material is then directed to either the spinning pump or the spin pack.
3. Spinning Pump for Metering & Die Pack
Spin pumps being precision units are required to convey the melt material evenly. The material must be fed to the spin pack centrally from the spin pump. Melt distribution with filtration and subsequent transport to the die-plate holes must be designed in such a way that there are no stagnation points in the flow and the melt emerging from holes has the same residence time in the die pack.
4. Cooling & Filament Forming
The molten monofilaments emerging from the die pack are cooled and formed in a quenching water bath. The monofilament diameter not only depends on hole size of nozzle plate but the distance between die pack and water interface.
5. Godet Unit for Parallel Guiding
Take-off rollers guide parallel monofilaments to the next step.
6. Hot Water Bath for Filament Stretching
The water drawing bath is essential for drawing monofilaments made from certain materials, either for process stability reasons or to achieve special characteristics that require drawing or pre-drawing.
7. Aspiration
This device is used for water removal.
8. Hot Air Oven for 2nd Filament Stretching
The hot air oven is used to heat the monofilaments for drawing.
9. Hot Air Oven for Filament Annealing
This process involves relaxing the monofilaments to shrink or maintain the required properties and diameter.
10. Oil finishing unit
The unit applies a thin layer of oil or lubricant onto the monofilament's surface, enhancing its smoothness, reducing friction, and facilitating downstream processing and handling.
11. Winding
Monofilament winding is a manufacturing process where a single-strand filament, often made of plastics or fibers, is systematically wound onto spools or reels in a controlled manner, creating a tightly wound coil for storage, transportation, or subsequent processing.
The monofilament extrusion process requires expertise, precision, and in-depth knowledge of polymers and manufacturing techniques. With advancements in technology and continuous research and development, this process continues to evolve, offering new possibilities and improvements in monofilament production. By understanding and optimizing the monofilament extrusion process, manufacturers can ensure the production of reliable and superior monofilament products.
If you would like to learn more about monofilament extrusion, we invite you to explore our recently published blog post on "How to Choose a Monofilament Extruder?". Additionally, you can find detailed specifications and product introductions through our Monofilament Extrusion Line. Stay up to date on the latest trends in monofilament yarn making machines by reading our article on "Monofilament Yarn Making Machine Trends for 2023". And of course, if you have any specific inquiries or want to discuss your customization requirements, feel free to contact us and speak with our experts.
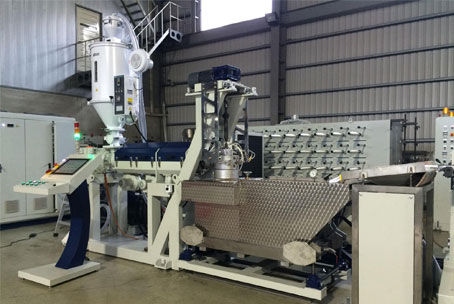
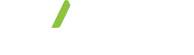
Taibao City, Chiayi County 61251, Taiwan
Phone: +886 5 2376175
E-Mail: [email protected]